Artykuł sponsorowany
Jakie są techniki identyfikacji i oznaczania części maszyn podczas demontażu?
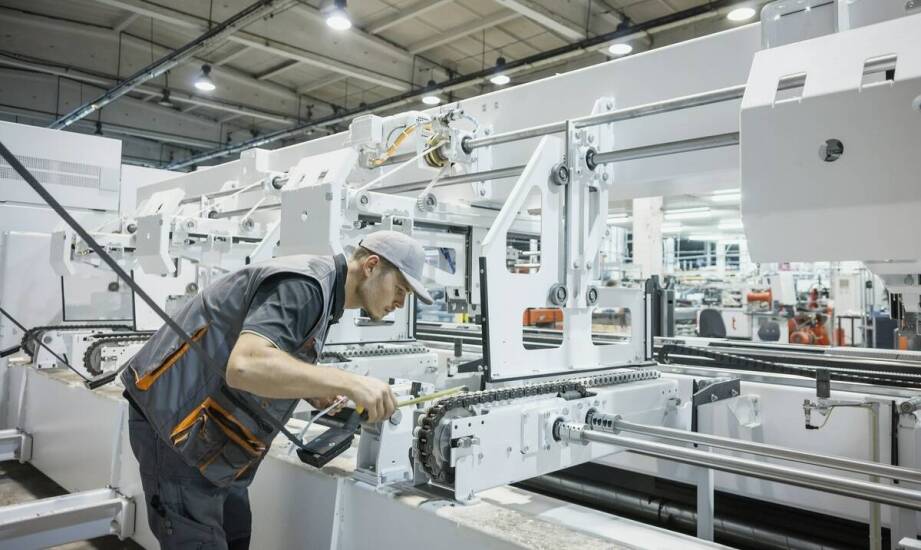
Demontaż maszyn przemysłowych to proces wymagający precyzji, doświadczenia i odpowiednich technik. Aby zapewnić sprawną relokację linii produkcyjnych czy całych zakładów przemysłowych, niezbędne jest właściwe oznaczenie i identyfikacja poszczególnych części maszyn. W artykule przedstawiamy cztery kluczowe techniki stosowane w tym celu.
Katalogowanie i etykietowanie części
Pierwszym krokiem w procesie demontażu maszyn w Rzeszowie jest dokładne katalogowanie i etykietowanie wszystkich elementów maszyny. Oznacza to nadanie unikatowego numeru lub kodu każdej części, co ułatwia późniejsze odnalezienie jej miejsca w konstrukcji. Etykiety mogą być wykonane z różnych materiałów, takich jak papier, plastik czy metal, a ich wybór zależy od specyfiki danej maszyny oraz warunków, w jakich będzie przechowywana.
Fotografowanie i dokumentowanie procesu demontażu
Dokumentowanie procesu demontażu za pomocą fotografii pozwala na utworzenie wizualnej instrukcji montażu, co znacznie ułatwia późniejszą rekonstrukcję maszyny. Zdjęcia powinny być wykonane z różnych perspektyw, uwzględniając zarówno szczegółowe ujęcia poszczególnych elementów, jak i ogólny widok całej konstrukcji. Ważne jest również, aby fotografie były opisane i posegregowane według kolejności demontażu.
Tworzenie schematów i rysunków technicznych
Opracowanie szczegółowych schematów i rysunków technicznych maszyny przed rozpoczęciem demontażu pozwala na zrozumienie jej budowy oraz funkcjonowania poszczególnych części. Dzięki temu można zaplanować proces demontażu w sposób efektywny i bezpieczny. Schematy i rysunki powinny zawierać informacje o wymiarach, kształtach oraz zastosowanych materiałach, a także oznaczenia poszczególnych elementów zgodne z etykietami.
Wykorzystanie oprogramowania do zarządzania procesem demontażu
Współczesne oprogramowanie do zarządzania procesem demontażu pozwala na skuteczne planowanie, monitorowanie i kontrolowanie prac związanych z relokacją maszyn przemysłowych. Dzięki nim można tworzyć bazy danych zawierające informacje o poszczególnych częściach maszyn, ich lokalizacji czy statusie. Oprogramowanie umożliwia również generowanie raportów, analizowanie postępów prac oraz komunikację pomiędzy członkami zespołu.